Exploring the World of Plastic Mold Manufacturing
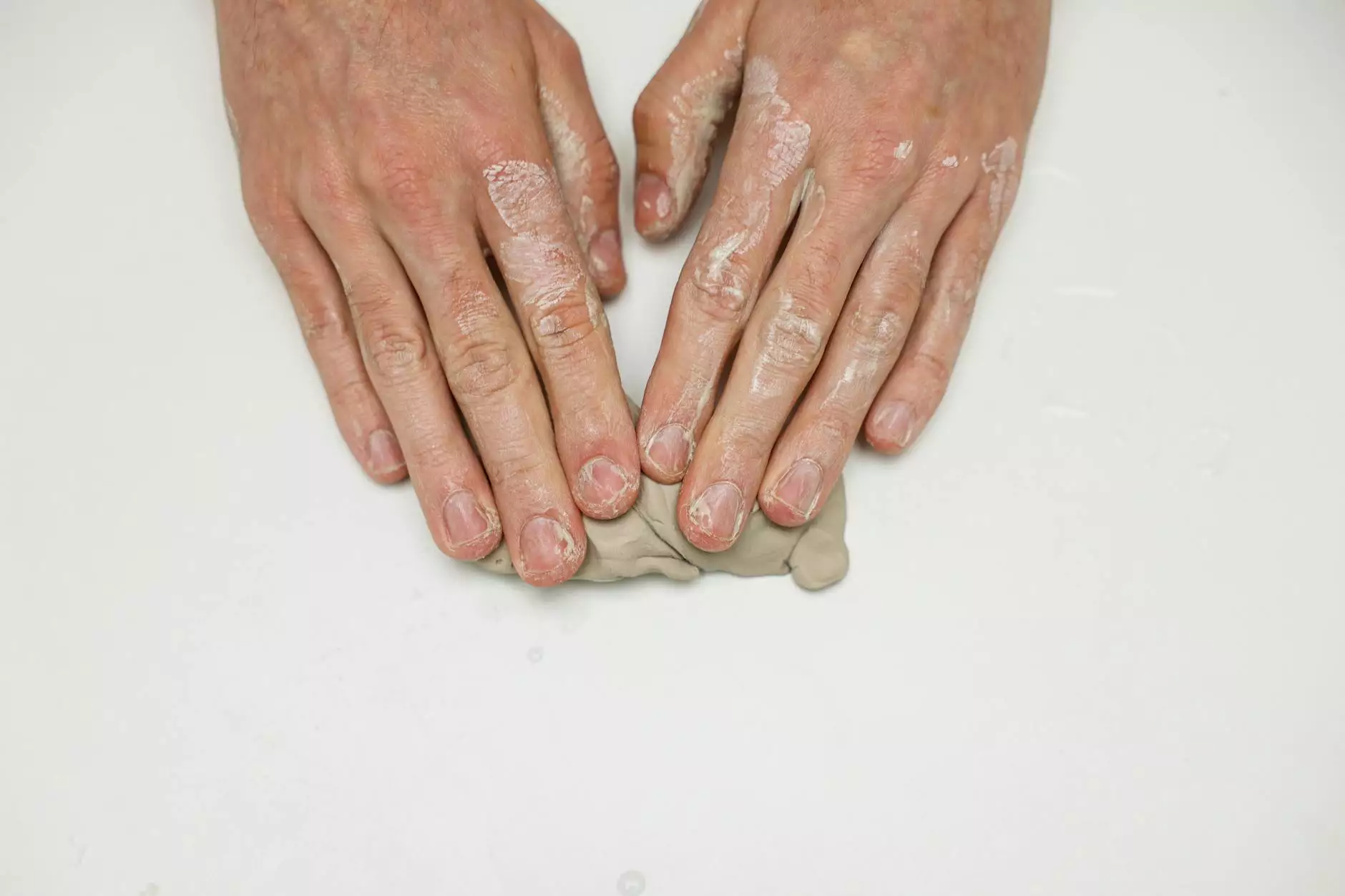
In the realm of industrial production, plastic mold manufacturing stands as a pivotal process that underpins advancements across various sectors. This intricate process involves the creation of molds to shape plastic materials, allowing businesses to produce a myriad of products efficiently and cost-effectively. In this article, we delve into the importance, processes, innovations, and applications of plastic mold manufacturing, with a particular focus on how Deep Mould defines excellence in service delivery within the Metal Fabricators domain.
The Importance of Plastic Mold Manufacturing
Plastic mold manufacturing is crucial for industries ranging from automotive to consumer electronics. The demand for precision, quality, and efficiency is ever-growing, making an understanding of the processes and technologies involved essential for manufacturers. Here are some key reasons why plastic mold manufacturing is vital:
- High Volume Production: Plastic molds enable the mass production of complex shapes in a consistent and efficient manner.
- Cost Efficiency: Although the initial investment in mold creation is significant, the long-term savings from producing high volumes with minimal waste make it financially advantageous.
- Design Flexibility: Molds can be designed to create intricate designs that meet specific functionality and aesthetic requirements.
- Material Versatility: A wide range of plastics can be molded to suit different applications, further enhancing the versatility of this manufacturing process.
Understanding the Processes Involved in Plastic Mold Manufacturing
The journey of plastic mold manufacturing begins with a comprehensive understanding of customer requirements. This section outlines the typical processes involved:
1. Design Phase
The initial step in plastic mold manufacturing is the design phase. This phase includes:
- Conceptual Design: Developing initial concepts based on customer specifications.
- 3D Modeling: Utilizing CAD (Computer-Aided Design) software for creating detailed 3D models of the required mold.
- Simulation: Running simulations to test mold functionality and predict performance.
2. Fabrication of Molds
Once the design is finalized, the next step involves:
- Material Selection: Choosing the appropriate material for mold fabrication (e.g., steel, aluminum).
- Machining: Employing CNC (Computer Numerical Control) machinery for precision cutting and shaping of the mold components.
- Surface Treatment: Enhancing durability through surface treatments, such as coating to resist wear and corrosion.
3. Injection Molding Process
After the mold is fabricated, it's ready for the injection molding process, where:
- Material Loading: Plastic resin pellets are heated until they become molten.
- Injection: The molten plastic is injected into the mold under high pressure.
- Cooling: The injected resin cools and solidifies within the mold.
- Ejection: Once set, the molded part is ejected from the mold for further processing.
Innovations in Plastic Mold Manufacturing
The landscape of plastic mold manufacturing is continuously evolving. Innovations are crucial not only for improving efficiency but also for enhancing product quality. Key innovations include:
1. Advanced Materials
Modern manufacturing techniques have led to the development of high-performance plastics that offer enhanced durability, heat resistance, and aesthetic appeal. Manufacturers now use sustainable and biodegradable materials to address environmental concerns.
2. Automation
The incorporation of robotics and automation in plastic mold manufacturing has transformed efficiency levels, reducing labor costs and improving precision in processes. Automated systems can handle everything from material management to product quality checks.
3. 3D Printing of Molds
3D printing technology has emerged as a promising alternative for creating mold prototypes. This method significantly decreases lead times and allows rapid iterations of designs, enabling manufacturers to respond swiftly to market demands.
Applications of Plastic Mold Manufacturing
Plastic mold manufacturing serves a broad spectrum of industries. Here are some notable applications:
1. Automotive Industry
Automakers leverage plastic parts for their lightweight and corrosion-resistant properties. Common components include:
- Dashboard assemblies
- Exterior panels
- Under-the-hood components
2. Consumer Electronics
With the rapid evolution of technology, consumer electronics require precision molded parts such as:
- Casings for smartphones and tablets
- Connectors and buttons
- Internal components for hardware devices
3. Medical Devices
The healthcare sector relies heavily on plastic mold manufacturing for:
- Disposable surgical instruments
- DNA testing kits
- Drug delivery systems
Choosing the Right Partner for Plastic Mold Manufacturing
Collaborating with a skilled and experienced partner is critical in ensuring the success of your production needs. Here are some factors to consider when selecting a plastic mold manufacturing company:
1. Expertise and Experience
Choose a partner with a proven track record in the industry. Experience translates into the ability to handle unexpected challenges and deliver quality products.
2. Technological Capabilities
Ensure that the manufacturer leverages the latest technology for design, fabrication, and production processes. Advanced capabilities can improve efficiency and reduce lead times.
3. Quality Assurance Processes
A robust quality assurance system is vital to uphold product integrity. Look for manufacturers who implement stringent testing at various production stages.
4. Customer Support
Strong customer support can make a significant difference in your collaboration. Choose a partner who offers comprehensive support throughout the project cycle.
Conclusion
Plastic mold manufacturing is a cornerstone of modern industrial production, offering unparalleled efficiency, precision, and versatility. Companies like Deep Mould are at the forefront of this industry, pushing the boundaries of innovation and quality in service delivery within the Metal Fabricators category. By understanding the processes, innovations, and applications associated with plastic mold manufacturing, stakeholders can better appreciate its impact and opportunities for growth. As industries continue to evolve, so too will the methodologies and technologies surrounding plastic mold manufacturing, shaping the future of production for years to come.