Die Casting: An Essential Overview of the Metal Fabrication Process
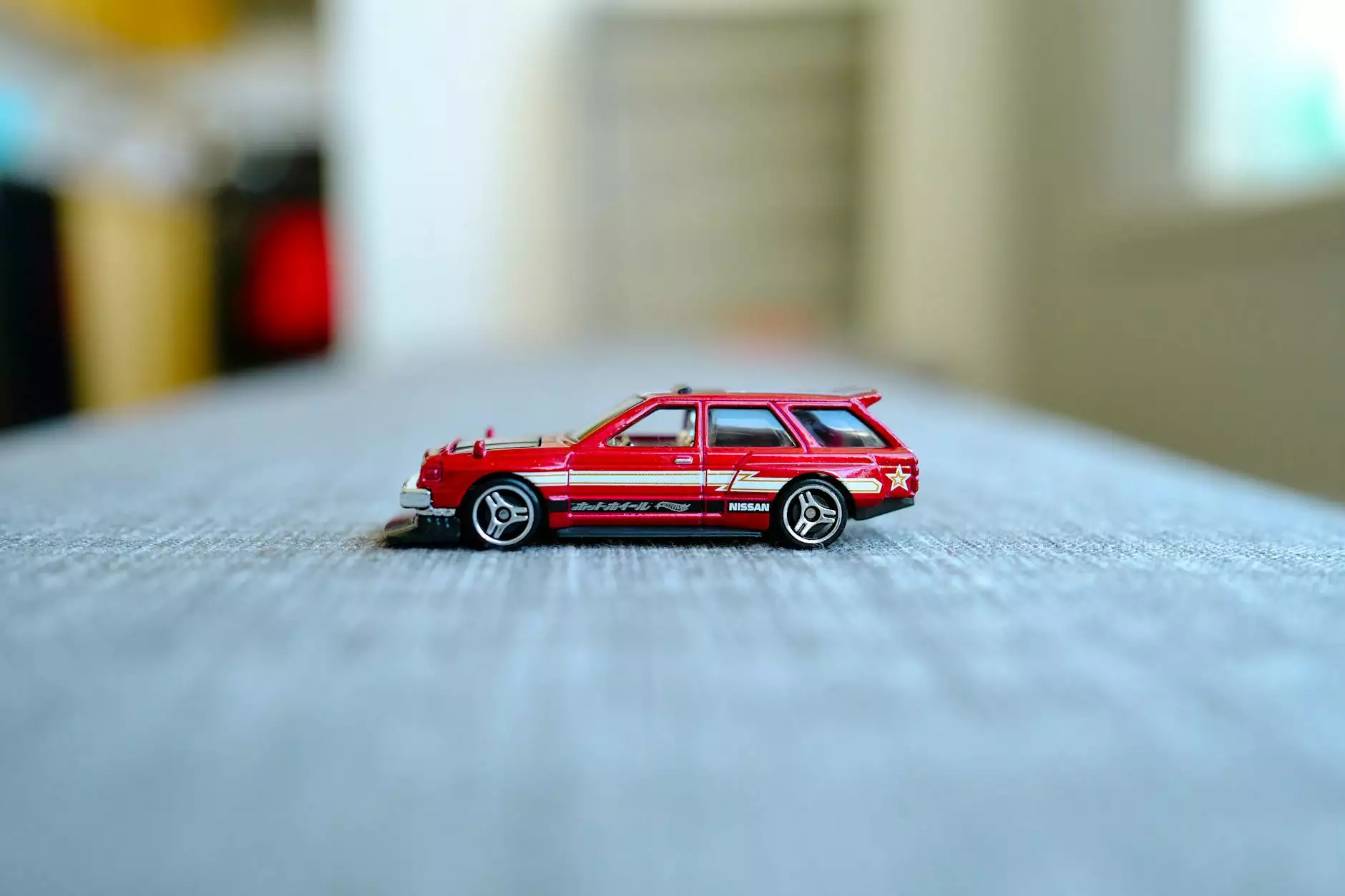
In the world of metal fabrication, die casting stands out as one of the most efficient and reliable methods for producing complex shapes with high precision. This article explores the intricacies of die casting, its benefits, applications, and why it is a cornerstone for businesses in the manufacturing sector, particularly at Deep Mould.
What is Die Casting?
Die casting is a manufacturing process that involves forcing molten metal into a mold cavity under high pressure. The molds, known as dies, are made from strong materials capable of withstanding the pressure and heat involved in the process. This method is widely used for producing metal parts with intricate designs and a high degree of accuracy.
The Die Casting Process
The die casting process can be broken down into several key steps:
- Preparation of the Die: The first step involves preparing the die, which is usually made from steel and consists of two halves – the core and cavity.
- Melting the Metal: The chosen metal, typically aluminum, zinc, or magnesium, is heated until it reaches a molten state.
- Injection of Molten Metal: The molten metal is injected into the mold cavity at high pressure, ensuring that it fills all intricate designs.
- Cooling: Once the metal cools and solidifies, the die is opened, and the finished part is ejected.
- Finishing: The part may undergo additional finishing processes, such as trimming, machining, or surface treatment, to meet specifications.
Benefits of Die Casting
The use of die casting in metal fabrication brings numerous advantages:
- High Precision: Die casting provides extremely accurate dimensions, making it ideal for producing complex parts.
- Smooth Surface Finish: Parts produced through die casting have a smooth surface, reducing the need for extensive finishing.
- Reduced Waste: This process minimizes material waste compared to other casting methods, which is essential for cost-efficiency.
- Quick Production Rates: Die casting allows for high-volume production, making it suitable for mass manufacturing.
- Versatility: The process can be used with various metals and alloys, enabling a broad range of applications.
Applications of Die Casting
Die casting finds applications in various industries due to its versatility:
Automotive Industry
In the automotive sector, die casting is widely used to produce components such as engine blocks, transmission housings, and other structural parts. This method ensures the lightweight nature of parts, contributing to fuel efficiency while maintaining strength.
Electronics
Manufacturing electronic housings and components require high precision. Die casting is ideal for creating enclosures and connectors that protect sensitive electronics while ensuring proper heat dissipation.
Aerospace
The aerospace industry demands extremely high tolerances and reliability. Die casting is used to manufacture parts for aircraft engines and structural components, where safety and performance are critical.
Consumer Goods
Many consumer products, such as appliances and tools, incorporate die casting components due to the attractive finish and durability they offer.
Why Choose Deep Mould for Die Casting Services?
At Deep Mould, we understand that the success of any manufacturing process hinges on precision, quality, and efficiency. Here’s why we stand out in the realm of die casting:
State-of-the-Art Technology
We employ the latest technology and equipment in our die casting process, ensuring that we produce high-quality components that meet or exceed industry standards. Our skilled engineers and designers work diligently to optimize every step of the process, from die design to final finishing.
Customization
One of our key strengths at Deep Mould is the ability to customize the die casting process based on specific client needs. We collaborate closely with our clients to understand their requirements and deliver tailored solutions.
Comprehensive Quality Control
Quality is our top priority. We implement rigorous quality control processes throughout the manufacturing cycle, ensuring every part we produce meets our strict standards and client specifications.
Environmental Considerations
As sustainability becomes increasingly important in manufacturing, die casting offers several environmental benefits:
- Recycling: Metals used in die casting can be recycled and reused, minimizing resource consumption.
- Energy Efficiency: The high-speed nature of die casting reduces energy consumption compared to traditional casting methods.
- Less Waste Production: The precision of die casting means that less scrap is generated, leading to a more sustainable manufacturing process.
Conclusion
Die casting is a vital process in the world of metal fabrication, providing unmatched precision, efficiency, and versatility. With its wide-ranging applications across various industries, it remains a favorite choice for manufacturers. At Deep Mould, we are committed to delivering exceptional die casting services that not only meet but exceed client expectations. As industries evolve, our adaptability and commitment to quality ensure that we remain at the forefront of the precision engineering sector.
For more information about our die casting services and how we can assist your business, visit our website at Deep Mould today.